Технологическая схема получения карбида кремния
Существует масса изобретений и запатентованных способов производства карбида кремния, вариантов конструкции печей и состава сырьевых материалов, например в дуговой печи, где дуга горит между двумя электродами, изготовленными из смеси кварцевого песка и углерода, синтез в плазме и т.д. . Однако, только ачесоновский способ получения применяется в современных производствах с разницей в конструкции и габаритах электропечей, применяемых сырьевых материалах и некоторых других технологических деталях. Такое продолжительное существование способа Ачесона можно объяснить простотой его осуществления, дешевизной и гарантией получением продукта достаточно высокого качества.
Технология промышленного производства карбида кремния может быть представлена нижеприведенной схемой на рис.7
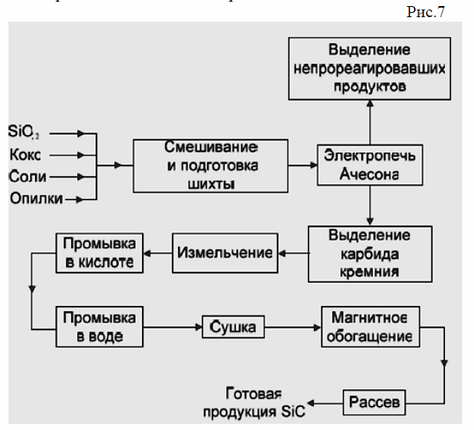
Состав и количество сырьевых материалов предопределено вышеприведенными теоретическими аспектами образования карбида кремния. При этом процесс получения карбида кремния описывается балансовой реакцией восстановления SiO2 углеродом:

В практике производства карбида кремния принят модуль шихты, теоретическое значение которого определяется следующей формулой:

При получении карбида кремния модуль реакционной шихты М принимают 37,5-38,0.

где Снк – массовая доля углерода в навеске нефтяного кокса:
Сл - массовая доля углерода в навеске лузги
Св.ш. - массовая доля углерода в навеске возвратной шихты;
SiO2кв.п. – массовая доля SiO2 в навеске кварцевого песка;
SiO2в.ш. - массовая доля SiO2 в навеске возвратной шихты
SiO2а - массовая доля SiO2 в навеске аморфа
SiO2кв.п. - массовая доля SiO2 в навеске кварцевого песка к керну;
Массовая доля углерода в нефтяном коксе С в процентах:
С = 100 - массовая доля золы × 1,4-массовая доля летучих веществ- массовая доля серы
Для восстановления полуторных оксидов металлов, находящихся в золе, массовая доля золы увеличивается в 1,4 раза.
Как следует из приведенных реакций, шихта для получения черного карбида кремния, состоит из углеродистого материала, кварцевого сырья, возвратной шихты, аморфа и выгорающего наполнителя в виде древесных опилок или лузги подсолнечника (риса) . В шихту для получения зеленого карбида кремния дополнительно вводят поваренную соль.
Углеродистые материалы для выплавки карбида кремния, должны обладать высокой реакционной способностью, достаточной механической прочностью, высоким электросопротивлением, содержать минимальное количество золы. Этими качествами обладают древесный уголь, нефтяной кокс, некоторые сорта малозольного каменного угля и т.п.. Однако нужно отметить, что полностью всем предъявляемым требованиям к восстановителю не удовлетворяет ни один из названных материалов.
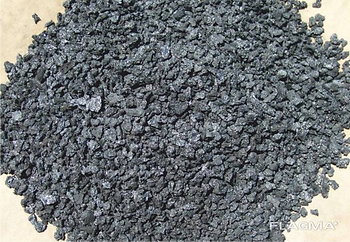
Из всех перечисленных материалов нефтяной кокс имеет самое низкое содержание золы, обладает достаточно высокой пористостью (до 46 %) и высокой реакционной способностью. Наиболее технологичным является нефтяной кокс с содержанием влаги не более 5,0%, золы не более 0,8 %, летучих не более 10,0 % и серы не более 3%.
Крупность частиц нефтяного кокса должна быть 0—2 мм с содержанием фракции 0—1 мм не менее 80%. Это обусловлено тем, что скорость образования карбида кремния в существенной мере определяется величиной реакционной поверхности углеродистого компонента и возрастает с увеличением этой поверхности.
В качестве кварцевого сырья применяются кварциты, крупка, высокочистые кварцевые пески.
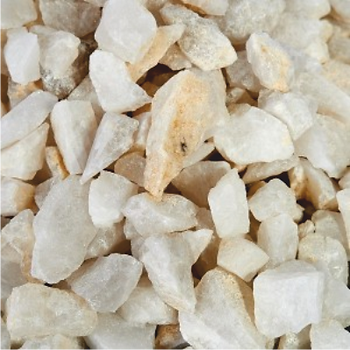
Кварцит—это горная порода, состоящая из зерен кварца, сцементированных между собой в основном кремнеземом. К химическому составу исходного сырья я предъявляются высокие требования по содержанию SiO2 – не менее 99%, массовой доли оксида железа Fe2O3 – не более 0,3%, оксида алюминия AL2O3 – не более 0,4. Кроме того, массовая доля глинистой составляющей не должна превышать 2%.
Предпочтительная крупность кварцевого сырья 1,0—10,0 мм. Допускается применение кварцевого песка крупностью 0,25—1,0 мм.
Кварцевое сырьё, не отвечающее указанным требованиям, соответствующим образом перерабатывается (обогащается). Как правило, для удаления примесей сырье ограничиваются его и отмывкой водой от глинистых "составляющих.
Более высокая крупность частиц кварцевого песка по сравнению с частицами нефтяного кокса обусловлена тем, что при малой крупности кварцевого сырья в ходе процесса синтеза SiC возникает нежелательное явление — факеление, вызывающее увеличение тепловых потерь, запыленность атмосферы и снижение выхода готового продукта. Во избежание процесса факеления частицы Si02 должны быть крупнее частиц нефтяного кокса не менее чем в 3 раза.
Поваренная соль осуществляет вывод соединений алюминия из зоны реакции за счет образования летучих хлоридов последнего, но её присутствие в шихте приводит к увеличению тепловых потерь и возрастанию расхода электроэнергии на 10—15 % по сравнению с производством черного карбида кремния. В шихту вводят до 2 % поваренной соли (ориентировочно на каждую десятую долю процента окиси алюминия ).
Древесные опилки или лузга являются основным порообразующим компонентом, используемым для придания шихте газопроницаемости. Недостаток выгорающей добавки в шихте приводит к снижению газопроницаемости и нарастанию давления внутри печи, образованию факелов — интенсивного выделения раскаленных газов, состоящих из окиси углерода и паров кремнезема.
Основные технологические процессы производства карбида кремния
Все применяемые в мире аппаратные схемы производства карбида кремния объединяет то, что процесс происходит в печах сопротивления различных конструкций, где горизонтальный нагреватель (керн), выложенный из углеграфитового материала, окружен реакционной и наполнительной шихтой. Тип, объём и мощность применяемых печей выбирается исходя из объёмов выпуска , способа получения карбида кремния и технического уровня предприятия.
Условно, по конструкции основного агрегата, аппаратные схемы формируются на основе стационарных или подвижных электропечей.
Стационарные печи имеют пониженную стоимость и повышенный срок службы. для стационарных печей практически нет ограничений веса, габаритов и, соответственно, мощности. Однако, при их эксплуатации все переделы производства, кроме подготовки сырья, осуществляются на одной площадке. Каждый передел обладает своей спецификой в отношении механизации и удаления вредных выбросов. Это требует отделения рабочих зон различных печей, привлечения отдельных кранов и множества средств механизации. Это целесообразно на больших печах мощностью более 10 Мвт.
На постсоветстком пространстве нашли применение только самоходные электропечи небольшой мощности (3…5Мвт), которые позволяют механизировать процесс и на всех переделах локализовать выбросы. Но очевидно, что такие процессы себя изживают из-за значительных теплопотерь в процессе синтеза, низкого выхода продукта и затрат на обслуживания печей.
Типовой технологический процесс производства карбида кремния
Процесс можно разделить на следующие этапы :
подготовка исходных материалов и шихты, загрузка печи, электротермический передел (плавка), охлаждение печи, разборка печи, охлаждение блока, сортировка блока.
Общая схема производства приведена на нижеследующей схеме производства. (рис.8)
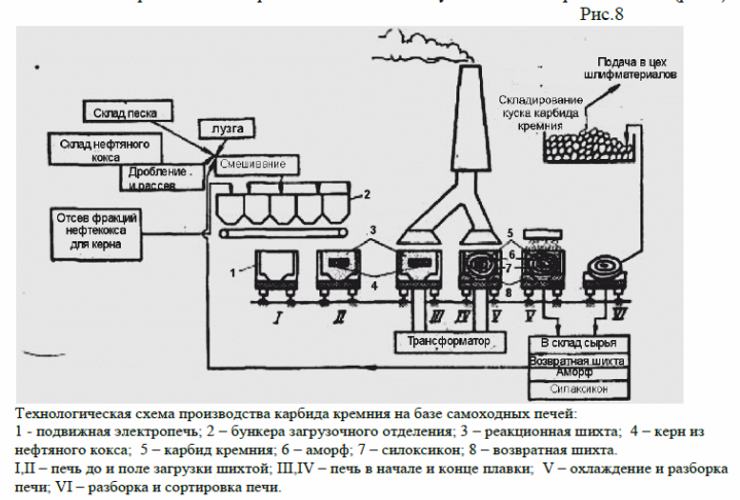
Подготовка шихты предусматривает дробление, грохочение и рассев сырьевых материалов, опробование и дозирование компонентов шихты в загрузочные бункера соответствующего отделения.
Электротермический передел процесса производства (загрузка печей и плавка) производится в печах сопротивления, конструкция которых представлена на рис 9.
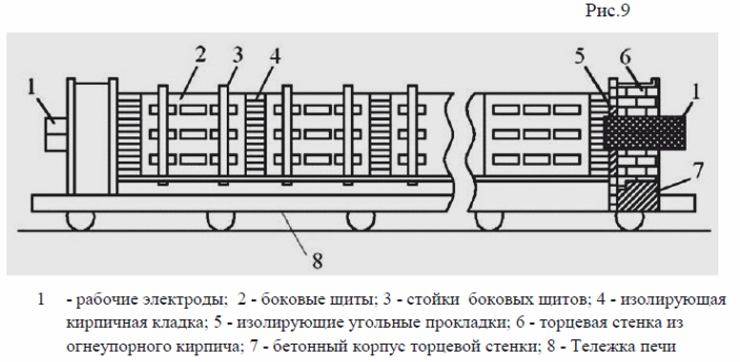
Подвижная печь сопротивления состоит из пода, боковых и торцовых стенок. Под печи выполнен из обычного шамотного кирпича, выложенного в гнездах чугунных кассет. Боковые стенки печи выполнены перфорированными щитами, устанавливаемыми по краям .конструкции пода. Щиты удерживаются в вертикальном положении стойками, которые входят в соответствующие гнезда печной рамы. Между щитами выкладываются изолирующие слои из шамотного кирпича. По концам рамы печи установлены торцовые стенки шамотного кирпича, в которые заделаны пакеты угольных электродов. На наружную часть электродов установлены контактные плиты, к которым на болтах прикрепляются шины, подводящие ток от печного трансформатора. Нагревательным элементом печи служит керн — центральная часть загрузки из нефтяного кокса, который разогревается при прохождении тока.
При загрузке печи выполняются ряд последовательных операций : загрузка шихты на подину печи; загрузка шихты до уровня керна; установка керновых щитов и укладка керна, с уплотнением контактных зон; загрузка шихты по бокам керна и извлечение керновых щитов; загрузка шихты сверху керна. После загрузки печи (рис.10) она перемещается в плавильную ячейку, подключается к трансформатору и начинается плавка.
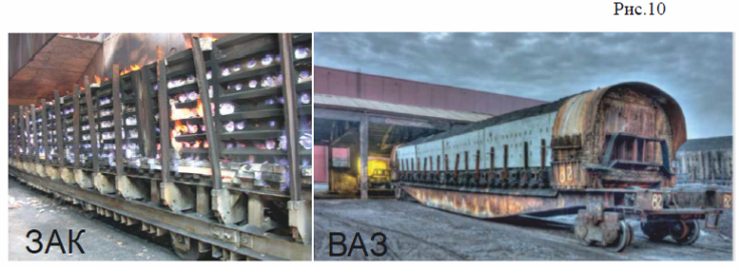
Работа электропечей для производства карбида кремния характеризуется значительным изменением сопротивления керна в процессе работы. В начале работы печь включают под напряжение. Полная мощность достигается примерно через 3 ч работы. В дальнейшем сопротивление печи значительно падает как за счет разогрева керна, так и за счет увеличения его сечения вследствие разложения части продукта, прилегающего к керну. Для поддержания постоянной мощности понижается напряжение на печи, в связи с чем используемые для питания печей однофазные трансформаторы оснащены автоматическими переключателями ступеней под нагрузкой.
Включение печи производят на мощности 1500 кВА. Через 15—20 мин после включения печи начинается выделение газов, которые поджигаются по всей поверхности печи во избежание взрывов и отравлений. Примерно через 8—10 ч после включений печь догружается теплоизоляционной шихтой для заполнения объемов, освободившихся в результате уплотнения и усадки шихты по мере протекания процесса. Продолжительность процесса определяется общим расходом электроэнергии на кампанию. Отключенная печь остывает обычно на воздухе в течение двух суток. Распределение мощности на печи для печи 3500 кВА представлены в таблице 1.
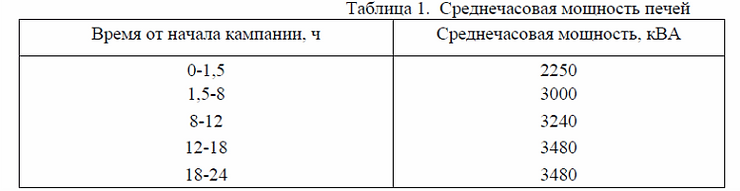
После охлаждения печи приступают к ее разборке, заключающейся в снятии боковых стенок и удалении непрореагировавшей шихты и слоя силоксикона. В случае необходимости применяют орошение печей водой, что значительно сокращает продолжительность общего охлаждения. Сортировку блока карбида кремния производят от периферии печи к ее центру, в первую очередь обрубают сростки аморфа с силоксиконом, затем взламывают блок карбида кремния, на сортировочных столах очищают куски карбида кремния от остатков кернового материала и аморфа. После уборки очищенного карбида кремния из печи извлекают керновой материал и складируют его в специальные кюбели. Затем взламывают, извлекают и сортируют нижнюю часть блока. Оставшуюся на подине подовую шихту и силоксикон без разделения извлекают и направляют на переработку в склад возвратных материалов. Очищенный и отсортированный продукт собирают в кюбеля и направляют в склад готовой продукции.
Производство карбида кремния указанным способом характеризуются следующими показателями: расход электроэнергии на 1 т продукта для карбидов кремния черного 7000—8500 кВт-ч, зеленого 8000—10 000 кВт-ч, расход кварцевого сырья 1750—2100 кг и нефтяного кокса 1000—1500 кг.. В печь загружается до 80 т шихтовых материалов, а получают до 10 т куска карбида кремния, 25—40 т возвратных материалов и до 25 т газообразного продукта (окиси углерода, летучих, паров воды). В структуре себестоимости карбида кремния до 30 % занимают сырьевые материалы, до 50 % — электроэнергия, до 20% —остальные расходы.
Причины значительных энергозатрат, невысокого качества и низкого выхода конечного продукта объяснимы. Из-за небольшого размера реакционной зоны, образующийся в процессе карботермического восстановления монооксид кремния SiO не успевает полностью прореагировать и в значительных количествах удаляется с печными газами, вызывая потери кремния и загрязняя окружающую среду. В прикерновой зоне (в интервале температур 2000-2300°С) происходит разложение карбида кремния на кремний и углерод, что увеличивает его потери. Таким образом, получают технический карбид кремния, загрязненный примесями углерода, оксида кремния, с выходом не более 15%.
Эти недостатки могут быть исключены за счёт использования стационарных печей большого объёма. Для снижения себестоимости карбида кремния и энергоемкости процесса рядом производителей производится утилизация тепла и энергии отходящих газов. Использование этой энергии за счет создания конструкции закрытой печи, улавливание и утилизация тепла отводящих газов позволяет снизить энергоемкость процесса на 30—40 %.
Практика применения стационарных печей небольшой мощности изжила себя из-за тех же недостатков, что и самоходных печей отечественных производителей. Параметры процесса плавки, режимы, электрооборудование печей практически не отличалось. Разница заключалась только в конструкции печей (рис. 11), производительности процесса и качества исходного сырья.
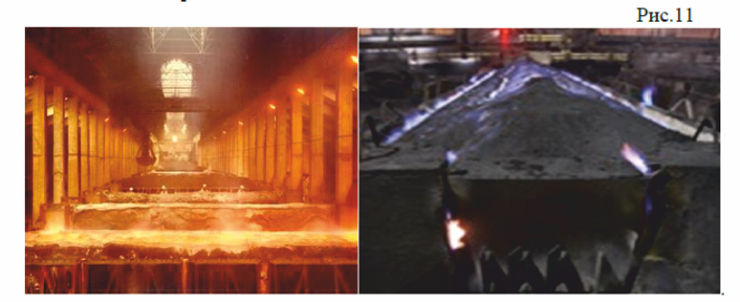
Современные производства основаны на буртовых печах большой мощности, с утилизацией выбросов и полной системой енергообеспечения. Подобные производства имеются в Германии (фирма ESK-SIC GmbH, в США (фирма «Вашингтон Миллс»), в Южной Африке (фирма «Сублайм») и др.. Синтез карбида кремния производится в стационарных штабель-печах (буртовых) большого размера, что позволяет получить карбид кремния более высокого качества, в части размеров кристаллов, чистоты материала и правильности формы, по сравнению с небольшими передвижными печами.
Типовая схема производства фирма ESK-SIC GmbH представлена на нижеследующем рисунке 12.
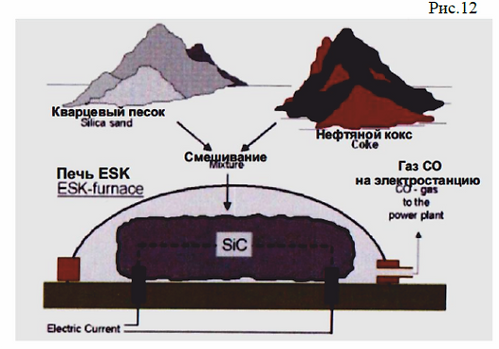
Увеличение теплоизоляционного слоя за счёт размеров штабель-печи позволяет использовать специальное укрытие в виде плёнки, которая обеспечивает улавливание отходящих газов, которые используются для производства электроэнергии в качестве топлива. Таким образом, решается одновременно как проблема защиты окружающей среды. Общий вид типовой штабель печи представлены на рис. 13.
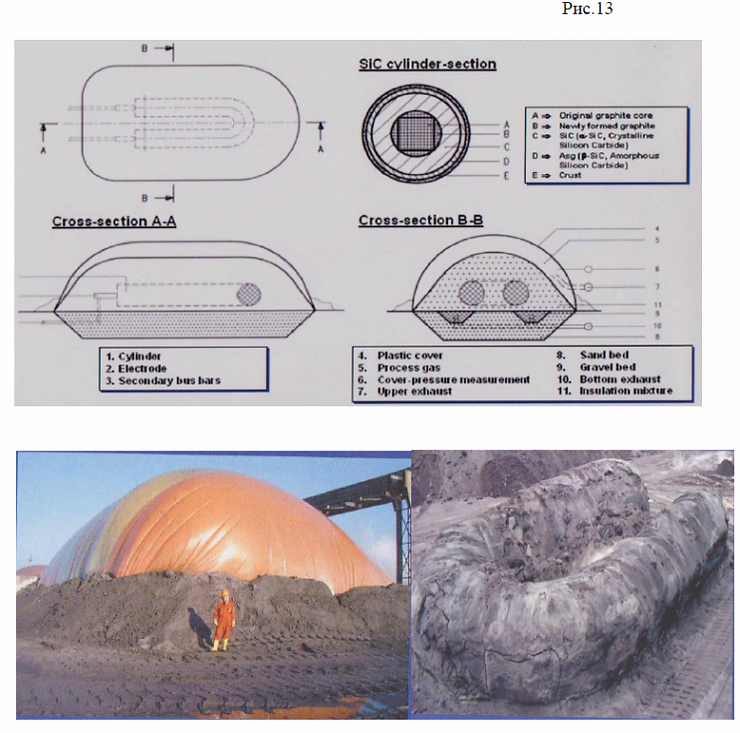
Технологические параметры процесса не является публичной информацией, но суть процесса не отличается от вышеописанной ранее технологической цепочки, а параметры процесса прогнозируемы.
Области применения карбида кремния
Карбид кремния SiС из-за высокой твердости и превосходных абразивных свойств используется в основном для изготовления шлифматериалов, которые используются для всего спектра абразивного инструмента на жёсткой и гибкой Его применяют также для изготовления карбидкремниевых огнеупоров на кремнеземистой, алюмосиликатной и нитридной связках. По своим электрофизическим свойствам SiС занимает промежуточное положение между алмазом и кремнием..
На основе карбида кремния получают нагреватели (силиты и глобары) для печей сопротивления. В теплоэнергетике карборунд применяют в составе огнеупорных масс в качестве заполнителя для футеровки ошипованных экранов топок энергетических котлов. Плитками из карбида кремния футеруют гидроциклоны, которые применяют при обогащении железных, марганцевых и других руд.
Карбид кремния используют в составе композиционных жаростойких материалов используемых в космической технике.
Зарубежные исследователи сосредоточивают усилия на изучении карбида кремния как возможного материала для конструкций передней стенки термоядерных реакторов. Остаточная радиоактивность SiС через 106 с после снятия нейтронного потока снижается до уровня активности углерода и практически в любой момент характеризуется величиной на несколько порядков меньше, чем остаточная активность алюминия и коррозионностойкой стали.
Карбид кремния выступает в качестве топлива для изготовления стали в конвертерном производстве. Он чище чем уголь, что позволяет сократить отходы производства. Также может быть использован для повышения температуры и регулирования содержания углерода. Использование карбида кремния стоит меньше и позволяет производить чистую сталь из-за низкого уровня содержания микроэлементов, по сравнению с ферросилицием и сочетанием с углеродом. Карбид кремния используют и для раскисления жидкой стали.
Подобно другим высокотвердым керамическим материалам (оксид алюминия и карбид бора), карбид кремния используется как компонент композитной брони, применяемой для защиты вооружения и военной техники, а также в виде составного элемента слоистой брони керамика/органопластик противопульных жилетов. В бронежилете «Кожа дракона», созданном компанией Pinnacle Armor, используются диски из карбида кремния
Первыми электрическими устройствами из SiC были нелинейные элементы вентильных разрядников для защиты электроустановок от перенапряжений. Карбид кремния в разрядниках применяется в виде материала вилита - смеси SiC и связующего. Также на основе карбида кремния делают варисторы.Эти элементы должны были обладать высоким сопротивлением до тех пор пока напряжение на них не достигнет определенного порогового значения VT, после чего их сопротивление должно упасть до более низкого уровня и поддерживать этот уровень, пока приложенное напряжение падает ниже VT..
Карбидкремниевые абразивные материалы.
Карбид кремния, как абразивный материал, содержит 98,5 % и более SiC, кристаллизующегося в основном в гексогональной структуре α -SiC. При температуре 1900—23000 C происходит перекристаллизация β-формы в α-форму.
Физические и химические свойства α и β карбида кремния и их политипов не имеют заметных различий. Однако, только карбид кремния α-SiC (гексагональной структуры) является абразивным материалом и имеет соответствующие свойства.
При плавке карбидов кремния сопутствующих минералов не образуется, однако в материале остается определенная часть непрореагировавших исходных материалов — восстановителя, в основном в виде графита, а также восстановленных из окислов до металла кремния и железа.
Различают два основных типа карбида кремния для шлифовальных материалов: зелёный и чёрный. ГОСТ предусмотрены для зелёного марки 63С и 64С, чёрного марки 53С и 54С. Металлургический карбид кремния является исходным материалом для производства фракций с массовой долей SiC не менее 88 %.
Шлифовальные материалы карбида кремния выпускаются в виде: шлифзерна, шлифпорошков и микрошлифпорошков. Основные их параметры представлены в нижеследующих таблицах 2…6.
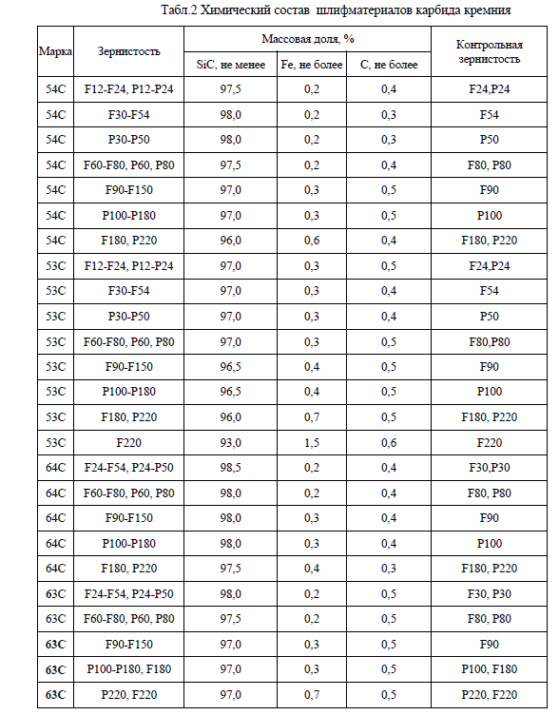
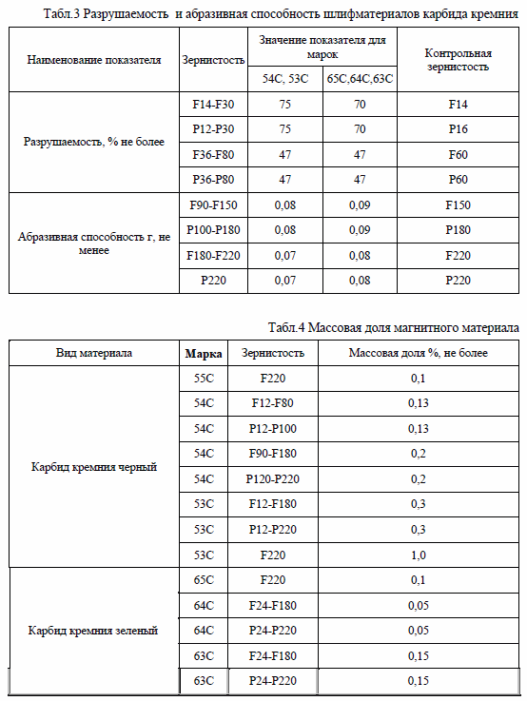
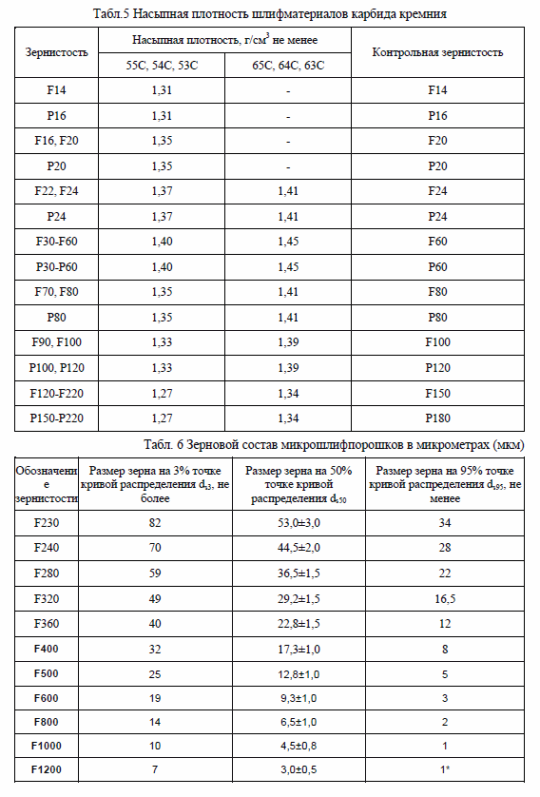